An electronic skin with cutting-edge sensitivity tracking a broad range of body motion has been created using liquid metal and a rigid nacre-inspired chromium-copper and silver underlayer.
Electronic skins are flexible, stretchable and self-healing devices that may one day form the basis of wearable and implantable sensors that monitor motion and physiological data, or give sensation feedback to prosthetics or robotics.
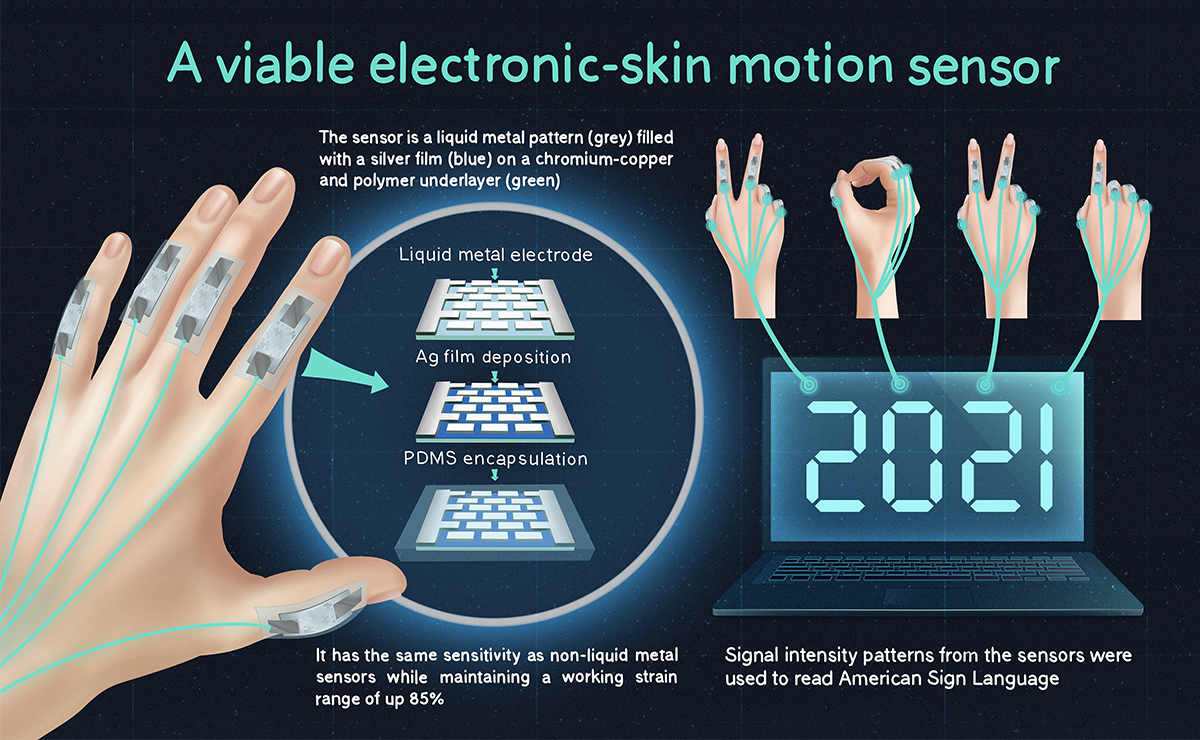
If ‘electronic skin’sensors can be designed to that they are highly flexible and sensitive, they could form the basis for wearable devices that collect data from active humans or robots.
In May 2021, Tsinghua’s Lei Liu, Hongwei Zhu, Guisheng Zou, and their colleagues, described an exceptionally strain tolerant and sensitive electronic skin based on liquid metal and a shell-inspired chromium-copper and silver supporting structure.
“We improved the sensitivity of liquid metal-based strain sensors by two orders of magnitude while maintaining a wide (>85% strain) working range,” explains Liu. The team tested their device by accurately interpreting sign language in English and Chinese, by sensing finger motions. It’s the first time, to Liu’s knowledge, that a sensor based on a liquid metal or a liquid metal composite has achieved comparable sensitivity as other state-of-the-art sensors.
Cracking e-skin
Liquid metals are popular electronic skin materials because they have strong electrical and thermal conductivity, stretchability and biocompatibility. But liquid metal-based electronic skins haven’t typically been able to achieve great sensitivity as electromechanical sensors, because their resistance change is normally insensitive during mechanical stimuli due to the fact that cracks form much less often in liquid metals.
Solid metal film cracking has been an established strategy to achieve high-sensitive electrochemical sensors. Although it appears a promising way to improve the sensitivity of liquid metal-based sensors by incorporating crack-sensitive films, it typically only works for limited strains, beyond which the cracking becomes so extensive that the sensor is not able to conduct a current.
“In our work, we propose a unique brick-and-mortar architecture to cope with this issue,”explains Liu.“This architecture consists of a biphasic pattern, which is the liquid metal with a chromium-copper underlayer as the‘bricks’, and a silver film as the‘mortar’”. The researchers took inspiration from the natural material nacre, also known as mother-of-pearl, which has a very high fracture toughness due to a combination of calcium carbonate platelets (the‘bricks’) and a polymer (the‘mortar’).
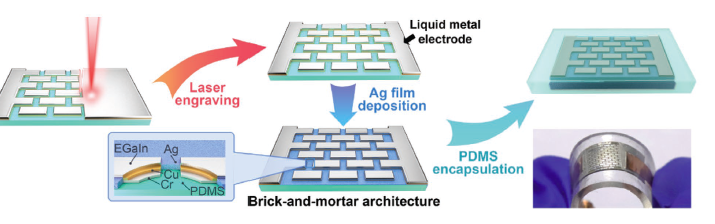
To make the sensor a laser forms a pattern in liquid metal (grey) coated over a chromium-copper underlayer on a polymer base (green). A silver film (blue) is deposited within the pattern. This sensor is then encased in polydimethylsiloxane (PDMS), a polymer containing carbon and silicon widely used for making microfluidic chips.
Strong, flexible foundation
The liquid metal was first coated over a chromium-copper underlayer supported on a flexible polymer, and then removed with a laser to form a pattern around which the silver film was deposited.
The rigid chromium cells regulate local strain, avoiding the formation of cut-through cracks in the silver film and instead promoting the formation of small cracks and buckling, which maintains electrical conductivity and ensures a wide working range. In a simple silver layer, cut-through cracks appear already at a strain of 20% and induce electrical disconnection. In the engineered structure, even at 50% strain, cut-through cracks barely started appearing. The separation between the liquid metal pockets prevents the formation of continuous liquid metal paths, while letting the liquid metal create crack-free regions during strain.
To test the sensor, the researchers used it to detect hand gestures to identify a phrase in American Sign Language, and English and Chinese sentences in Morse code.
“The sign language test is a good demonstration of the applicability of electronic skins,”remarks Liu.“By sensing finger motions, different signs can be distinguished, and thanks to the connection with information processing terminals their meaning can be extracted.”
The next steps in the development of this type of sensors include the ability to distinguish between different types of movement, such as bending and stretching, which often co-exist. Because the device uses low-cost materials that are already commonly used in flexible electronics and standard processing methods, there is potential for scalable and economical fabrication of sensors based on this design.
Reference
Feng, B., Jiang, X., Zou, G., Wang, W., Sun, T. et al Nacre-Inspired, Liquid Metal-Based Ultrasensitive Electronic Skin by Spatially Regulated Cracking Strategy Advanced Functional Materials 31(29), 2102359 (2021)
doi: 10.1002/adfm.202102359